
Trucks take a trip through a flooded roadway while leaving from an Amazon shipment station in Carlstadt, New Jersey, U.S., on Tuesday, Oct. 13, 2020.
Bloomberg|Bloomberg|Getty Images
Consumers have actually pertained to anticipate when they purchase something online, it gets here in 2 days or less. With increasing unfavorable weather condition occasions like Houston's heatwaves, Florida's cyclones and other severe storms, it's getting more difficult to guarantee quick shipment.
Lots of logistics business have actually alerted about shipping hold-ups due to severe weather condition. Weather-related supply chain interruptions will cost the market an approximated $100 billion in 2024, according to Freight Waves. Freight options business Breakthrough, which concentrates on sustainable transport, carried out a study of 500 carriers and providers this year that exposed severe weather condition was mentioned as the leading transport obstacle.
“Shippers and providers continue to deal with a myriad of disturbances,” Breakthrough chief running officer Jenny Zanden stated in a declaration. “Last year, transport experts were concentrated on decreasing expenses as a way to get rid of unstable diesel costs. This year, sustainability and climate-related interruptions are driving the requirement for fuel performance and modifications to transport technique.”
The concerns are impacting essential international transport avenues, such as the Panama Canal, where dry spell conditions have actually pestered carriers. The problems are likewise increasing for the most significant sellers in the U.S. as they try to get provided to consumers and keep storage facilities and shops equipped.
In March, an anticipated snowstorm struck the Sparks, Nevada. It resulted in the closure of Donner Pass, which numerous chauffeurs utilize to pass through the northern Sierra range of mountains. Walmart was not able to dispatch its grocery shipment from its Sparks center as an outcome. It turned to predictive analytics and expert system to enhance last-mile techniques.
“We have now this innovation at our hand, which permits us to ensure that we continue to serve those consumers in the very best possible method, run those situations, and have those suggestions prepared so that we can begin acting in a much quicker method, instead of awaiting the occasion to take place and after that responding,” stated Walmart senior vice president Parvez Musani.
Walmart utilized its simulation platform constructed with expert system to develop a digital twin of its whole network. Predictive modeling enables the business to see how to respond to an unfavorable weather condition occasion, consisting of if there are shops or storage facilities in the weather condition course that require to be closed down and where those orders can be satisfied. In the Sparks storm, Walmart recognized 85 shops spread out throughout Nevada, California and Oregon that might be rapidly straightened to resolve the shipment coming from the Sparks. The system had the ability to discover 4 particular warehouse that might deal with the work, in addition to deal alternate driving paths to get products to consumers.
“Our objective is that by utilizing innovation and AI, we make it smooth for our clients where they do not see the effect of a few of this unanticipated occasion that occurred,
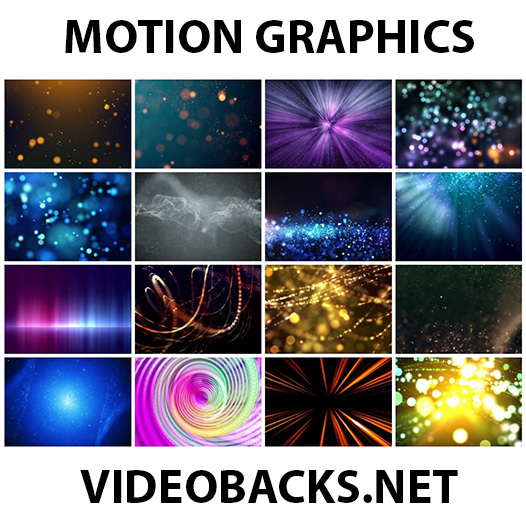